I bought a small MIG/MAG/TIG/MMA welder. Nice little unit for a Taiwanese job
After precisely 2 times dragging the welder, gas bottle, welding gear and accessories around the house I decided I needed a cart to put everything on.
I wanted a double shelf with both gas bottles at the back (and not slopping around like on most carts).
Around this time I also discovered that the biggest problem with the Welder was the cheap shite gas hoses and connectors. |
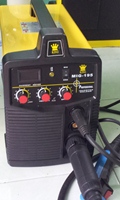 |
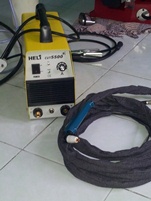 |
As I started to cut out the required steel for the cart, I quickly discovered that cutting a straight and long
line in a 1.5mm sheet is almost impossible with a angle grinder and a metal cutter wheel.
There was nothing for it, I had to have something better to do the job. Oxy/Acetylene is expensive and dangerous to store around the house..
Enter the Heli Cut5500...
A brilliant little 55 Amp, air driven, Korean made plasma cutter, capable of 10mm cuts.. and a whole lot better than those China units... |
Anyway back to the welder. I had to replace those horrid hosees and el cheapo clamps..
I bought Japanese, high quality, quick release connectors, and high quality hoses. After a bit of fuss removing the leaks from the regulator connectors (a bit of sanding), all was sealed and I was happy.
Those cheapo connectors had realy let me down, while welding the workbench I lost a lot of CO2. I could not hear the leak with the welder switched on. |
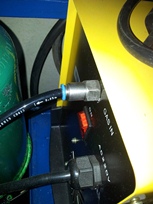 |
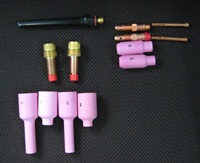 |
These shots show the MIG/MAG torch spares (with MAG be prepared to go through a lot of tips even using dipping paste)
The Tig Torch comes with a collet. I bought extra collets and tungsten tips.
I also bought several Gas Lenses and collets and assorted ceramics. Gas Lenses are a great investment and help a lot. |
I needed to purchase an Air Compressor to drive the Plasma Cutter.
These pics also show the Plasma Cutter consumables.
Finally some pics of 3mm sheet cut with the Plasma cutter. I had never used one before so I am slowly getting better, however I am thinking of making some sort of fitting to cut
circles and keep the nozzle off the steel as I cut. Of course a CNC frame would be nice!
Not that there is anything wrong with drag cutting, but for thicker steel it is better to have that 1-2mm space between nozzle and work. |
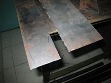 |
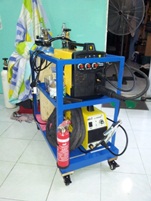 |
I ended up making the cart out of a combination of 1.5mm plate, 25mm x 2.5 angle and 25mm box steel.
The usual toxic Chrome and Zinc primer, finished with single pack enamel. Another blue item in the workshop.! Not many pics as I was too busy at the time for progress shots
I put on some locking castors and used bungee cord to keep the gas bottles tight. I added a small fire extinguisher for safety. I also added some steel hooks for retaining the torches
BTW thats the CNC mill in the background with the sheet over it.. Next Project! |